Sealcoating restores sun-bleached asphalt to its original black appearance, forming a barrier against water, oil, and other oxidizing substances. It also prevents fine cracks from forming in the asphalt and protects it from chemical penetration.
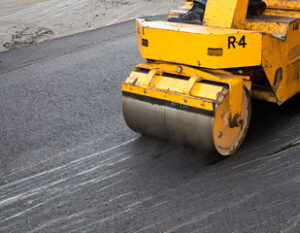
Wear long-sleeved shirts, pants, waterproof boots, and gloves when working with seal coating. Some Rochester NY Sealcoating contains petroleum-derived chemicals that can irritate skin.
Surface preparation is a critical step before any coating or adhesive can be applied to a surface. It removes any contaminants like dirt, dust, rust, and oil that could affect the performance of the coating once it is applied. It can be done using methods like laser cleaning, abrasive blasting, and chemical cleaning.
Abrasive blasting is one of the most common and effective methods for preparing surfaces for application of coatings. This method uses a blast of abrasive materials like sand, shot, and glass beads to thoroughly clean the surface while also roughing it up for adhesion. This is a critical part of the process because many coatings require a rough surface for optimal bonding.
Another common method of preparing surfaces is wet abrasive blasting. This involves using a hose with nozzle to spray water and abrasive mixtures onto the surface to thoroughly clean it while also roughing up the surface. This is also a good option for surfaces that cannot be blasted with dry media due to environmental restrictions or safety concerns.
The most important thing to remember is that every surface is unique and has different requirements for proper preparation. For example, if you are recoating a metal surface that has previously been coated with an epoxy or urethane coating it is critical to remove all traces of the previous coating before applying the new coating. This will ensure that the new coating adheres properly and prevent any cracking or blistering.
Some surfaces need a very rough surface to achieve good adhesion while others only require a very fine texture. This is why it is so important to fully understand the specifications of each job you work on and the final desired result.
The sealcoat acts as an adhesive layer that holds together any loose aggregate and fines in the asphalt, helping to keep it structurally sound. It also helps to protect the pavement from chemical penetration and slows down the oxidization process that damages the pavement and increases erosion. Getting the surface prep right is essential in both situations to ensure that your sealcoat lasts as long as possible and gives you the best value for your money.
Squeegee Application
Sealcoating protects the asphalt surface from the penetration and degradation of oil, fuel, chemicals, and salt. It is also beneficial for preventing cracking and premature deterioration, as well as preserving the value of your property. Regular sealcoating prevents the need for expensive paving and repairs, and can extend the life of your pavement significantly.
The squeegee application process allows us to pack the material into the cracks of rough or porous surfaces, giving your pavement a stronger bond. It can be performed using a ride-on sealcoating machine with squeegee attachments, or by hand with an individual squeegee tool. This method can take longer than spray application, but offers more control and a thicker application.
In addition, squeegee application is a great choice for restoring old or damaged concrete. It can be used on precast slabs, stamped or textured concrete, or in conjunction with a chip overlay. This method also works well on small areas where time is limited and a spray application would be too much work.
Both the squeegee and spray application methods have their pros and cons, but choosing the right one depends on your specific needs. The key is to choose a reputable and experienced contractor. It’s not the application technique that matters, but how it is managed.
Spraying is faster and allows crews to cover large areas in a fraction of the time it takes with a squeegee. However, the faster pace can lead to missed spots and a thinner overall application. Spraying can be problematic if the surface is too smooth and free from voids. The squeegee method is the best way to force the sealant into these voids, and provides a more consistent finish. In either case, the resulting finished product will enhance the longevity and beauty of your pavement. Both spray and squeegee applications require careful management to achieve the best results. We recommend a combination of both methods for the most comprehensive and cost-effective pavement maintenance solution. Regular agitation of the sealer tank and removal of the suction port when not in use will help prevent blockages.
Spray Application
Sealcoating isn’t just for aesthetics, it protects asphalt surfaces from heat and cold, water damage and oil spills. It also creates a rich dark color that enhances curb appeal and increases the value of your property. When it is done correctly, every few years, sealcoating can extend the life of your asphalt parking lot or driveway.
Properly prepping the surface is essential for successful sealcoating. The surface should be free of grease stains, raised areas, cracks and any other damage. If any of these items are left on the surface, they will prevent the new coating from adhering to the asphalt and creating a strong bond. Additionally, the surface should be dry before applying sealcoating to ensure proper curing.
While spray application is the most common method of applying sealer, some contractors use alternative techniques to apply the material. Brush application, for example, is heavily reliant on manual techniques and can leave streaks or uneven amounts of sealer on the surface. This is a result of the fact that the operator must manually adjust the valve settings, hoses and spray tip. Proper training helps the operator understand how to maintain consistent pressure, ensuring an even coat of sealant.
For smaller surfaces, a squeegee is the best way to spread sealer. Workers fill buckets with the sealer and then spread it across the surface using a squeegee. The squeegee method takes longer than spray application, but it can cover more area and is more effective at filling cracks and crevices.
Regardless of the application method used, it’s important that all equipment is properly maintained and trained for trouble-free operation. The filter pots, hoses and spray tips must all be of a quality that can handle high temperatures and pressure. Valves should be installed between the pot and hose to control the flow of the liquid and to reduce the amount of spray produced. A trained and experienced operator should know how to troubleshoot these issues to ensure optimal performance.
As with any construction job, it’s important to follow all safety protocols. Proper safety gear is essential, including rubber gloves and a face mask. A professional should be familiar with all the different aspects of his or her machinery, including how to maintain and inspect the pump and nozzles for leaks or other problems. A thorough safety training program will help the operator avoid any mishaps that could cause injuries or property damage.
Finishing
Once the surface is ready to be seal coated (all cracks and potholes have been repaired) it is time to start the process of applying the coal tar or asphalt emulsions. This should be done on a day where the weather is not raining and temperatures are above 60 degrees. Once the sealer is mixed it is applied with a squeegee or spray nozzle, depending on manufacturer recommendations. Once the application is complete, it will need to cure for at least 36 hours. If striping for parking spaces is required, it should be completed after the seal coat has cured.
When applied properly by a certified asphalt professional, sealcoating will increase the life of your blacktop for years to come. The jet-black finish is aesthetically pleasing, and the slip resistant properties will make your business more appealing to potential customers and reduce liability. This preventative maintenance will also save money in repair and restoration costs.
Asphalt sealcoating does not repair existing damage like cracks or potholes, but it will protect the surface from further deterioration, allowing you to get more life out of your investment. Sealcoating should be performed every other year to maintain a quality surface and prolong the life of your pavement.
The best time of the year for asphalt sealing is from Memorial Day through Labor Day, with a continued application up until the cold weather sets in. Sealcoat does not bond well to the surface below 50 degrees, so it is recommended that you perform your sealcoating project in optimal weather conditions.
Before beginning the sealing process, the asphalt should be brushed to remove any dirt, organic material or debris that has adhered to the surface. A wire brush may be used to loosen embedded material that has not been loosened by the cleaning process. This should be followed by a thorough power washing. The clean surface will allow the sealer to adhere and provide a more effective protective layer.
It is important to understand that asphalt sand is used in the mix for most sealcoats, along with water and some type of petroleum binder. The sand adds friction to the asphalt surface and helps to fill in small holes and depressions in the pavement. The petroleum binders help the asphalt to resist oxidation from the sun’s UV rays, and the harmful chemicals such as motor oil and gasoline that can eat away at it.